“備えあれば憂いなし” リスクアセスメントをやってみよう
(さんぽいばらき 第28号/2007年3月発行)
はじめに – 何故リスクアセスメントなのか
リスクアセスメントという言葉が、最近、あちこちの分野で聞かれるようになりました。文字通り解釈すれば「危険性 ( リスク ) の事前評価 ( アセスメント )」ということになります。産業安全、労働衛生の分野では、労働者の就業に係る危険性又は有害性 ( リスク ) を前もって見つけだし、それがどのくらい危険・有害であるかを評価したうえで、その評価に基づいてリスクを低減するための対策を検討するという一連の流れをさします。
では、何故、リスクアセスメントが必要なのでしょうか。それは、科学技術の進歩や経済的な発展により、生産工程の変化と複雑化し、それに伴う労働災害の原因の多様化したことに理由があります。従来、労働者の安全や健康の問題が起きないようにするための管理は、多くの国において、法規制で行われてきました。しかし、法律を制定するには、化学的にも明らかな事実が分かっていることが必要であり、実際の被害が発生した後でないと規制が実施できないなどの問題がありました。つまり、対策が後手にまわることが多く、さらには、作業工程の多様化や使用される設備や原材料、化学物質等の数が膨大になり、安全管理や衛生管理を法規制にだけ頼ることでは不十分なことは明らかになったからです。
このため、より一層自主的な責任ある行動が必要との認識にたって、実際に作業により起こりうる可能性のある有害・危険性の程度 ( リスク ) の程度を見積もり、その結果から得られるリスクの大きさを評価して、その程度により管理の内容を決めていくリスク管理が、より一層、重要になってきました。
改正労働安全衛生法に努力義務として規定
こうしたことが背景となって、昨年、労働安全衛生法が改正され、自主的に個々の事業場の設備、原材料、有害物等又は作業行動その他業務に起因する危険性又は有害性等の調査を実施し、その結果に基づいて労働者の危険又は健康障害を防止するため必要な措置を講ずること、いわゆる「リスクアセスメント」 (註1) が事業者の努力義務として規定されました (同法28条2 第1項)
また、法改正を受けて、昨年3月、厚生労働省は各事業場においてリスクアセスメントが適切かつ有効に実施されるよう、「危険性又は有害性等の調査等に関する指針」(以下「指針」という)を定めるとともに、化学物質に関しては「化学物質による危険性又は有害性の調査に関する指針」(以下「化学物質等調査指針」)を発表しました。これら指針は、安全衛生マネジメントシステムに関する指針においても、「法第28条の2第2項に基づく指針に従って危険性又は有害性等を調査する手順を定めるとともに、この手順に基づき、危険性又は有害性等を調査するものとする。」と位置づけているように、安全衛生マネジメントシステムの重要な要素となっています。
註1 「リスクアセスメント」は、狭義ではリスクの評価までをさしますが、指針では評価に基づき適切なリスク低減措置を実施するところまでを含んでいます。
これまでの安全衛生活動とリスクアセスメント

安全衛生活動の変遷・発展
何度も言うようですが、リスクアセスメントに基づく考え方は、安全衛生の分野では標準的な考え方になりつつあります。厚生労働省の調べでも、リスクをより客観的に評価する事業場の方が、そうでない事業場より労働災害発生率が低くなっています。
しかし、これまでの安全衛生活動は、「災害に学ぶ」ことで対策が立てられ、事前の災害対策についてはあまり多くは論じられてきませんでした。
右記に示しましたように、安全衛生活動は「安全第一」から始まり、「整理整頓」、機械設備の大型化等による潜在的危険性を排除する機械設備の「本質安全化」を経て、近年の労働災害防止活動は、潜在危険性の低減を目指すようになりましたが、危険又は有害性と人のかかわりによってリスクを評価するということまでは、あまり行われてきませんでした。
リスクアセスメントは、このかかわりの具合がどの程度のものであり、また相対リスクがどのレベルにあるかを調べること、すなわち、リスクの発生率や災害の重篤度(ひどさ)といった関数を使って数値で表す(厳密な数値で表すことは困難ですが、大雑把には可能です)ことにより、事前にリスクの大きさを評価し、その評価に従って対策の優先度を設定し、リスク低減対策の内容を検討するという、いわば事故の未然防止の考え方なのです。
なお、リスクの大きさを“評価する”と言っても、評価する人の価値観が入りますので、リスクの大きさを一般的、一意的に決めることはできません。従って、ある程度のあいまいさがつきまとうのは仕方なく、実務的には、数値化する際にもいくつかのクラスに分けると言った、半定量的な手法が行われています。
ちなみに、リスクとは「危害の発生率と危害のひどさの組合わせ」と定義されています。
リスクアセスメント(危険性又は有害性の調査)の手順 – 第1ステップは危険源の特定
リスクアセスメントには、実施すべき順番があります。まず、最初にやることは、設備、原材料、有害物等又は作業行動その他業務に起因する危険性又は有害性等を特定することです。これを「危険源の特定」ともいいます。
危険源の特定では、危険源を全て洗い出し、リストアップする作業が必要です。これは大事な作業ですが、見落としの可能性もあります。指針には、「危険性又は有害性の分類例 (註2) 」が掲載されていますので、これを参考に、危険源がどこにあるのかを調べればよいでしょう。これが第1ステップです。
なお、危険源の特定では、「予見可能な誤使用」といって“人間だいたいこうした誤りはするものだ”ということも考慮の中に入れておき、それを明確にしておくことも大事です。
註2 危険性又は有害性の分類例
- 危険性
- 機械等による危険性
- 爆発性の物、発火性の物、引火性の物、腐食性の物等による危険性
「引火性の物」には、可燃性のガス、粉じん等が含まれ、「等」には、酸化性の物、硫酸等が含まれること。 - 電気、熱その他のエネルギーによる危険性
「その他のエネルギー」には、アーク等の光のエネルギー等が含まれること。 - 作業方法から生ずる危険性
「作業」には、掘削の業務における作業、採石の業務における作業、荷役の業務における作業、伐木の業務における作業、鉄骨の組立ての作業等が含まれること。 - 作業場所に係る危険性
「場所」には、墜落するおそれのある場所、土砂等が崩壊するおそれのある場所、足を滑らすおそれのある場所、つまずくおそれのある場所、採光や照明の影響による危険性のある場所、物体の落下するおそれのある場所等が含まれること。 - 作業行動等から生ずる危険性
- その他の危険性
「その他の危険性」には、他人の暴力、もらい事故による交通事故等の労働者以外の者の影響による危険性が含まれること。
- 有害性
- 原材料、ガス、上記、粉じん等による有害性
「等」には、酸素欠乏空気、病原体、排気、排液、残さい物が含まれること。 - 放射線、高温、低温、超音波、騒音、振動、異常気圧等による有害性
「等」には、赤外線、紫外線、レーザー光等の有害光線が含まれること。 - 作業行動等から生ずる有害性
「作業行動等」には、計器監視、精密工作、重量物取扱い等の重筋作業、作業姿勢、作業態様によって発生する腰痛、頸肩腕症候群等が含まれること。 - その他の有害性
- 原材料、ガス、上記、粉じん等による有害性
リスクの見積り(第2ステップ)
第2ステップは、その危険源でどのくらいのリスクが発生するか、リスクを見積ることです。リスクとは、「危害の発生率と危害のひどさの組合せ」と定義しましたが、単純に言えば、危なさの度合いと考えて結構です。
リスクの見積りは、その危険源でどのくらいの割合で労働者が被災するかと言うこと(負傷又は疾病の発生可能性の度合い)と、被災したときの災害の程度(負傷又は疾病の重篤度)の2つを見積るのが一般的です。さらに、これを掛け合わせでリスクの大きさを評価します。実務的には、「発生可能性の度合い」と「重篤度」を点数化しておき、それらを乗じる(×)か、加算(+)して、リスクの大きさを数値化します。
リスクの評価と優先度の設定(第3ステップ)
第3のステップは、そのリスクが安全か否かの判定です。「安全」ということは、いいかえれば「許容可能なリスク (註3) 」のことです。一般的なやり方としては、リスクの大きさを4~5段階に分けて、そのうち一番低いリスクを「許容可能なリスク」に分類します。これ以上のリスクは「許容できないリスク」ということになり、これを低減する対策がとられることになりますが、これらのリスクも「極めて問題があるリスク」、「問題があるリスク」、「多少問題があるリスク」というふうに、程度によりランク付けするのが普通です。
実は、このリスクの評価がリスクアセスメントで最も難しいところです。というのは、前にも述べましたように、人のというより会社の価値観が入ってくるからで、社内の合意作りが大切になります。
註3 絶対安全がない以上、必ずリスクは残ります。何をもって許容可能とするかですが、一般には「その時代の社会の価値観に基づく所与の条件下で受け入れられるリスク」のこととされています。
リスク低減措置の実施(第4ステップ)
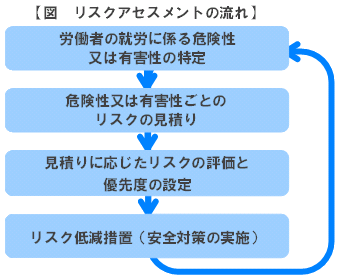
図 リスクアセスメントの流れ
最後のステップですが、安全と認められなかった、つまりリスクが大きすぎて「許容できないリスク」は、そのリスクを低減させる対策を講じなければなりません(当然にリスクの高い方から優先的に実施されなければなりません)。
しかし、安全対策を施しても完全にリスクがなくなる訳ではありません。そこで、リスク低減対策を実施後に、もう一度リスクの評価を行い、それでも「許容可能なリスク」に分類されないときは、残存リスクを明らかにするとともに、それが「許容可能なリスク」とされるまでは、リスクアセスメントの流れを繰り返すことになります。
リスクアセスメントの実施体制の整備
ヨーロッパ等では、既にこのリスクアセスメントが導入され、効果が確認されていますが、わが国では、このようなシステマチックな方法はあまり普及していませんでした。ですから、職場に導入するためには、実施体制を整備することがどうしても必要になります。
指針では、「総括安全衛生管理者等、事業の実施を統括管理する者(事業場トップ)に調査等の実施を統括管理させること」と述べていますが、トップによる導入の“決定”と“宣言”は必須です。なぜなら、リスクを許容する基準を最終的に決めるのは、トップにほかならないからです。また、企業活動を展開する上で、安全衛生というファクターは非常に重要ですが、そのためには安全を体系的に企業経営に組みこまなければならず、事業場トップが、リスクアセスメントの意味をきちんと認識しておく必要があります。
責任者と推進組織の明確化、教育訓練の実施
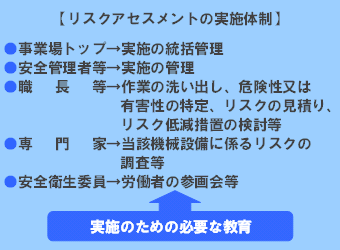
リスクアセスメントの実施体制
リスクアセスメントの導入が決定されたら、次に実施組織を明確にして、その責任者を決める必要があります。
実際には、安全管理者、衛生管理者等にリスクアセスメントの実施を管理させることになると思いますが、責任者と事務局及び推進組織(チーム)の役割分担の明確化が重要です。
また、事務局は、職場で正しくリスクアセスメントが実施できるように「運用マニュアル」を作成するとともに、推進チームに対して教育・訓練を行うことも必要です。
職長等や作業員も参加して
指針では、「作業内容を詳しく把握している職員等に危険性又は有害性の特定、リスクの見積り、リスク低減措置の検討を行わせるように努めること」と述べています。危険源を見つけ出すことを、危険源の特定あるいは同定といいますが、リスクアセスメントでは、危険源は全て見つけるという手順を踏みます。
しかし、膨大な数に及ぶ危険源を管理者だけで把握するのは困難です。そこで、危険なところを最もよく知っている職長等に、危険源の特定等を行わせるというのは、最も合理的な考えです。それでも危険源の特定に不安があれば、作業員全員が集まって意見を出し合い、他人が気付かなかったことを見つけ出すというようなことを、積極的に行うべきでしょう。現場の作業者の協力を得ることで、リスクに対する共通認識ができるという副次的な効果も期待できます。
リスクアセスメントの実施時期
リスクアセスメントの実施時期について、指針では、次のとおり述べています。
- 建設物を放置し、移転し、変更し、又は解体するとき
- 設備を新規に採用し、又は変更するとき
- 原材料を新規に採用し、又は変更するとき
- 作業方法又は作業手順を新規に採用し、又は変更するとき
- その他
これらの時期は、経験則上、労働災害発生の可能性が特に高いことが分かっています。
しかし、このほかにも労働災害が発生した場合や、社外における類似作業で災害が発生した場合にも実施するべきでしょう。また、既存の建設物等や現実に行われている作業方法等であって、それまで調査が実施されていないものについては、年次計画を作成し、順次リスクアセスメントを実施すべきです。
対象の選定、作業の洗い出し
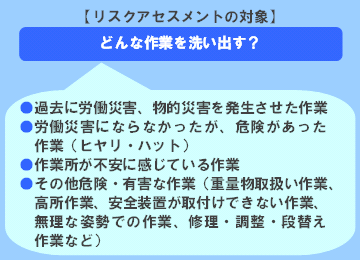
リスクアセスメントの対象
どの職場の、どの作業又は設備をリスクアセスメントの対象としたら良いのでしょうか。原則としては、運転前の「立上げ」から通常運転、不具合発生時の処理、定期メンテナンスはもちろんのこと、機械の移設・解体・廃棄等、職場に関連する全ての作業をリストアップしなければなりません。
この点について、指針では、リスクアセスメントの対象を「過去に労働災害が発生した作業、危険な事象が発生した作業等、労働者の就業に係る危険性又は有害性による負傷又は疾病の発生が合理的に予見可能であるもの」としています。しかし、明らかに軽微な負傷又は疾病しかもたらさないような作業は除き、過去に災害やヒヤリハット等がなくても、合理的に推定して負傷又は疾病が発生する可能性のある業務は全て対象になります。
また、おなじ作業でも、ベテランが就くか初心者が就くか、男性か女性か、あるいは身体能力の違いによって危険性又は有害性の程度・内容は異なってきますから、そうしたことも考慮に入れなければなりません。ちなみに、ベテランだから安全化というと、意外とベテランが安全装置を「殺して」いるケースも見られますから、そうでもありません。安全装置を故意に外すことによって発生する負傷も、予見可能な負傷ということが出来ます。
危険性又は有害性の特定
リスクアセスメントの対象となる作業等を選定した上で、各事業場における機械設備及び作業ごとに危険性又は有害性(危険源)を特定します。
リスクアセスメントでは、危険源を漏れなくリストアップすることが最も大切なことですが、見過ごすことも考えられます。危険源を見過ごさないためには、分類表などに則して即して危険源を特定するのがベターです。
先に示した「分類例」の、(1)の「機械等による危険性」には「押しつぶし、「せん断」、「切り傷」、「挟まれ・巻き込まれ」などが含まれます。先にあげた、安全装置を「殺すことなどは、(6)の「作業行動等から生ずる危険性」に含まれるかも知れません。
また、安全装置が使いにくかったり、エラーを誘発したりするような、人間工学的原則を無視した作業・設備も危険源に含まれますし、単調作業の連続による集中力の欠如や、深夜労働による居眠り等も危険性又は有害性への付加的影響として考慮する必要があります。
全員参加で危険源を見つけ出し、リスクアセスメントの記録を保存
危険性又は有害性の特定にあたっては、当該工程の作業者を参加させることが大切です。危険なところをよく知っている作業者が、自分で自主的に危険源を見つけ出したり、作業者全員が集まって意見を出し合ったりすることは、動機づけとしても有効です。
また、洗い出した作業、特定された危険性又は有害性(危険源)については、調査票に記録 (註4) しておく必要があります。
註4 記録すべき事項としては、次が考えられます。
- 作業名
- 特定された危険性又は有害性
- 見積もられたリスクと評価(措置の優先度)
- リスク低減対策
- 低減対策実施後のリスクの評価及び残存リスク対策
作業名 | 危険性又は有害性と災害 発生のおそれのある災害 |
既存の災害防止対策 | リスクの見積り | ||
重篤度 | 発見可能性 | リスク評価 | |||
穴あけ作業 (プレス2号機) |
光線式安全装置の側面から補助作業者の手が入る | 両手押しボタン及び光線式安全装置 | 重大 (4) |
可能性 大(3) |
高 (4) |
プレス作業 (プレス3号機) |
足元にスクラップが散乱し、つまずき・転倒等の危険 | 整理整頓を呼びかけている | 中程度 (3) |
可能性 中(2) |
中 (2) |
略 |
リスクの見積り
特定された危険源のリスクがどのくらいの大きさかを見つけ出すことを「リスクの見積り」といい、リスク低減対策の優先度を決定するうえで、大変重要な作業です。
リスクとは、「危害の発生率と危害のひどさの組合せ」ですから、リスクの見積りは、危害つまり負傷又は疾病の「発生の可能性」と危害の「ひどさ(重篤度)」を考慮して決めます (註5) 。また、化学物質による疾病の場合は、化学物質等の有害性及びばく露可能性の両者を考慮して見積ることになります。
さて実際に、どのようにしてリスクを見積るかというと、一般的には、危害の発生の可能性、危害のひどさ(重篤度)を数値化して、それらを関数として、次のように表現します (註6) 。関数については、かけ算と足し算の二通りがありますが、どちらでもかまいません。
リスク = 危害発生可能性の数値 + (又は×) 重篤度の数値
しかし、「危害の発生の可能性」といった抽象的なものを、どのようにして見積ったらよいのでしょうか。どのくらいの頻度で危害が発生するといったデータがあれば簡単かも知れませんが、実際にはそんなデータはありません。実は、リスクの見積りは、リスクを客観的に見ることが狙いですから、厳密な数値化は必要ありません。多少の曖昧さがつきまといますが、気にする必要はありません。
具体的には、危害発生可能性、重篤度等をいくつかの相対的な尺度(ランク)に分けて評価します。例えば、重篤度では、「致命的(5)」、「重大(4)」、「中程度(3)」、「経度(2)」というように、ランクと数値(カッコ)を決めます。危害発生可能性も、同じようにいくつかのランクに分けて評価します。
このように、厳密ではありませんが、半定量的な手法が現実には用いられています。ランク分けと点数の例を表1~3 (註7) に示しておきます。
註5 これに「作業の頻度」を加える例もあります。
註6 必ずしも数値で表す必要はなく、危害の重篤度と可能性を縦軸と横軸とした行列(マトリクス)によりリスクを見積る方法もあります。
註7 表1~3では、作業の安全度、危険作業の頻度、危害の重篤度の3つからリスクを評価しています。この様に、危害発生可能性を「作業の安全度」と「危険作業の頻度」に分けるケースもあります。この場合、相対的に「危害の重篤度」の比重を重くします。
作業の種類 | ほとんどない (危険を察知すれば回避できるもの。普通であれば考えられない事故。過去に事例なし。) |
可能性がある (会費手順を知っていれば危険を回避できるが、うっかりしていると事故になる。過去に事例がある。) |
可能性が高い (専門的な訓練を受けていなければ、注意していても事故になる。過去に何度となくある事例。) |
可能性が非常に高い (高い集中力を維持していないと災害になる。) |
点数 | 1 | 3 | 5 | 7 |
作業の別/点数 | 1 | 2 | 4 |
定常作業 | 1回/週未満 | 1回/週以上 | 1回/日以上 |
機械の清掃、点検調整、段替え等の作業 | 通常は実施することがない | 必要に応じて実施する | 日常的に実施している |
災害の程度 | 赤チン災害 | 不休災害 | 休業災害 (残存障害なし) |
残存障害あり・死亡災害 |
点数 | 1 | 3 | 6 | 9 |
リスクの評価
リスクアセスメントの基本的な流れ
危害の発生する可能性と危害の重篤度がわかれば、その組合せから、リスクを決めることは簡単です。危害発生可能性の点数と危害重篤度の点数を足し算(または掛け算)して、点数を求め、何点以下は「許容可能」、何点から何点までは「望ましくない」、何点以上は「許容できない」というようにリスク・ランクを評価するのです。表4に例を示しますから、参考にしてください。
現在、加算法が最も多く用いられていますが、より精緻にリスクレベルを求めたければ、様々な演算法がありますので、それを試せばいいでしょう。
その結果、リスクが許容可能であればリスクアセスメントは終了し、許容できない場合はリスク低減対策を実施し、再度、このプロセスを繰り返します。危険又は有害性の特定からリスクの見積り、リスク評価及びリスク低減対策の実施までの全プロセスが、リスクアセスメントです(流れ図参照)。
リスクの値は誰が決めるか
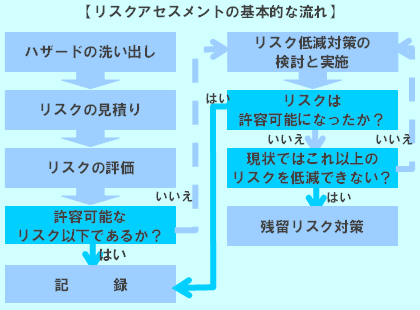
リスクアセスメントの基本的な流れ
リスクの評価は合理的で客観的な方法が望まれますが、実際は、関係する当事者が合議 (註8) して、ランクも点数も主観的に決めるものです。また、結果としてのリスクレベルのランク分けも、ランク間の境界はあいまいでファジーなものです。
リスクの見積りに関しては、単なる多数決や平均でなく、最悪のケースもふまえて論議し、基本的には関係者が「このくらいにしましょう」と納得することが大事だと思います。
註8 作業の洗い出しとリスクの見積りは、その職場に精通している監督者と作業者が中心となりますが、リスクの評価とリスクの除去・低減対策の議論は、監督者と安全スタッフ及び管理職が中心になると思います。
合計点 | リスク・ランク | 評価/対策(優先度) |
3~7 | I | 許容できるリスクレベルと判断。現状維持でも可であるが、なお、残存するリスクについての情報を作業者に提供する。 |
8~11 | Ⅱ | 多少の問題あり。非常停止装置や保護具の着用等の追加的安全対策を講じる。 |
12~15 | Ⅲ | かなり問題あり。第一義的には機械・設備の本質的安全化を実施する。当面、安全防護措置又は上記IIの措置を実施する。 |
16~ | Ⅳ | 重大な安全衛生上の問題あり。機械・設備の本質安全化を直ぐに実施する。また、リスクの低減が図られるまで作業禁止の措置を講じる必要あり。 |
リスク低減対策の検討、実施と優先順位
リスクアセスメントの結果、リスクが大きすぎて許容可能とはいえない場合は、リスク低減対策 (註9) を実施しなければなりません。
リスク低減対策にもいろいろな方法がありますが、これには決まった順番があり、下図のように1~4のステップを踏んで実施します。
最初にすべき対策(ステップ1)は、いわゆる「本質的安全設計」と呼ばれているもので、設計や計画の段階から労働者の就業に係る危険性又は有害性を除去又は低減する措置のことです。危険な作業をやめることや、より危険性・有害性の低い材料に代替することなども含まれます。
しかし、必ずしも本質的安全設計ができるとは限りません。その場合には、2番目のステップとして、「安全防護(工学的対策)」対策を実施します。具体的には、インターロックなどの安全装置、ガス・粉じん状の有害物質については局所排気装置を設置する等の工学的対策です。つまり、危険又は有害なものをガードで囲ってしまい、人を近づけないようにすることです。これを「隔離の安全」ともいい、様々な安全装置が開発されています。
安全防護対策を実施しても、まだ十分にリスクを下げられない場合は、3番目のステップとして「管理的対策」を講じます。「管理的対策」とは、上記2つの対策により除去しきれなかった危険性又は有害性に対し、マニュアルの整備、立ち入り禁止措置、ばく露管理、警報設置、二人組性の採用、教育訓練などにより作業者を管理することで、リスクを低減しようとするものです。
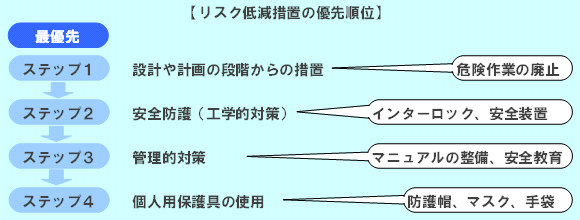
リスク低減措置の優先順位
しかし、これでもリスクは残存することもあります。4番目のステップは「個人用保護具の使用」によるリスク低減で、いわば労働者本人が気を付けなければならないものです。つまり、労働者に安全装置の使用や保護具や保護衣等の使用を義務づけるもので、これが一番信頼おけないものであることは、労働衛生担当者は身にしみて分かっているはずです。
ここで重要なことは、対策をステップ1~4の順番で適用しなければならないということです。ステップ1やステップ2を飛ばして、ステップ3を実施してもリスク低減対策を実施したとはいえません。
なお、法令に定められた事項がある場合には、事業者は、それを必ず実施する必要があることは言うまでもありません。また、死亡、後遺障害又は重篤な疾病をもたらすおそれのあるリスクについては、適切なリスク低減対策の実施に時間を要する場合でも、暫定的な措置を直ちに講ずる必要があることに留意なければなりません。
註9 安全対策と言ってもいいのですが、近年“絶対安全はない”という考えのもと、リスク低減という言い方が使われています。
リスク低減措置の必要性の判断基準
リスクには、許容できるレベルのものがある一方で、許容できないのでリスク低減措置を実施しなければならないレベルのものもあります。では、許容できないリスクについて、どの程度リスク低減対策を実施すればよいのでしょうか。実は、これは大きな問題で、残ったリスクの大きさを許容できるがか、はたして「安全」といえるか、頭を悩ますことになると思います。
残念ながら、絶対的な許容可能なリスクの定義はありません。先に述べたように、「その時代の社会の価値観に基づく所与の条件下で受け入れられるリスク (註10) 」を許容可能なリスクといいます。ということは、許容可能な定義は時代々々によって変わりますし、機械の使用目的や被害を受ける人の立場によっても違います。
従って、リスク低減措置を検討するにあたっては、リスク低減に要する負担がリスク低減による労働災害防止対策と比較して大幅に大きく、両者に著しい不均衡が発生する場合を除き、合理的に実行可能な限り、出来るだけリスクを下げる努力をしなければなりません (註11) 。
つまり、改善の効果がリスク低減の費用に全くつりあっていないような場合のみ、残存するリスクは許容されることになります。
註10 例えば、自動車と航空機では、求められる安全対策のレベルがかなり違っているように思えます。それは、自動車があまりにも便利なために、私たちは自動車事故による死亡率が多少高くとも、それを許容可能なレベルと受け入れているからかもしれません。このように、許容可能なリスクレベルは、経済的な利便性からも影響を受けています。
註11 社会的・経済的要因を考慮に入れ、合理的に達成可能な限りリスクを低く抑えるべきであるというALARA(As low as reasonably achievable)の原則が適用されると考えられます。
注 「いばらき労働基準」に掲載した原稿に加筆、修正したものです